PRODUCT
صفحة رئيسية>منتجات>
crusher plant maintenance articles
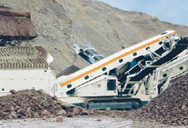
Construction, Working and Maintenance of ... - Practical
2018年12月26日 Information about crushing technology, construction, working and maintenance of crushers for bulk materials is given in this article. Crushing Technology. There are four basic ways to reduce size of a material: by impact, by compression, by shear or by attrition. Most crushers employ a combination of all these crushing methods.2017年8月24日 The Reliability of the crusher influences the productivity of the plant. The purpose of this paper is to focus the application of reliability centered maintenance with an aim to improve the reliability of the cone crusher. reliability tools failure modes and effects analysis and total time to test-Plot are explored in support of the study.Reliability centered maintenance of cone crusher: a case 2019年1月2日 Though traditional maintenance practices exist in crushing plants, a methodical analysis of failure trend is imperative to improve operational reliability of this critical equipment. The present paper deals with failure analysis of rock crusher and its critical components using total time on test (TTT)-plot and other statistical tools.Failure rate analysis of Jaw Crusher: a case study Sādhanā
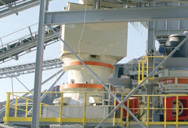
Understanding three different types of crusher maintenance
2018年3月15日 Listed below are three completely different types of crusher maintenance that must be thoroughly understood regardless of the crusher type being used. Preventive Implementing a preventive maintenance program is the best method of keeping a crusher in good operating condition for a long period.2014年2月25日 A cone crusher is used in mineral processing plant as a secondary or tertiary type rock crusher. In this case study, explored the general objective of the failure modes and effects analysis (FMEA) and FTA analysis work is to evaluate the application impact of the reliability centered maintenance (RCM) methodology on a power Reliability centered maintenance of cone crusher: a case studyFully utilizing the latest preventive crushing and screening machine maintenance technology can help save aggregates production business owners big money annually. After all, crushers and screens are critical assets that keep their businesses running smoothly and efficiently. Lokotrack® ST3.5™ mobile screen.Preventive crusher and screen maintenance - Metso
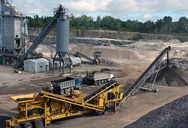
Maintenance and Optimization of Crushing Plants:
2023年9月2日 Crushing plant downtime can cause significant financial loss. Discuss the importance of effective planning of scheduled maintenance downtime to minimise production disruptions. Explain the benefits of a detailed maintenance schedule, coordination with suppliers and availability of necessary spare parts.2014年5月14日 The article presents a method to combine crushing plant simulation and optimisation with quality and economic considerations in order to successfully study alternative configurations of the...Field monitoring and performance evaluation of crushing plant 2020年1月1日 In effort to remedy this, this article considers relevant maintenance issues at early stages of product development and presents a novel modular methodology based on the simultaneous...Preventive Maintenance Scheduling by Modularity Design
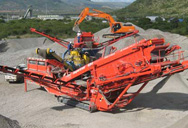
Seven Critical Maintenance Items For Mobile Crushing Plants ...
2023年10月26日 The seven critical maintenance items discussed in this article, including lubrication systems, conveyor belts, crusher components, screening components, electrical systems, dust control and suppression, and emergency systems, are essential for keeping mobile crushing plants operational, efficient, and safe.2018年12月26日 Information about crushing technology, construction, working and maintenance of crushers for bulk materials is given in this article. Crushing Technology. There are four basic ways to reduce size of a material: by impact, by compression, by shear or by attrition. Most crushers employ a combination of all these crushing methods.Construction, Working and Maintenance of ... - Practical 2017年8月24日 The Reliability of the crusher influences the productivity of the plant. The purpose of this paper is to focus the application of reliability centered maintenance with an aim to improve the reliability of the cone crusher. reliability tools failure modes and effects analysis and total time to test-Plot are explored in support of the study.Reliability centered maintenance of cone crusher: a case
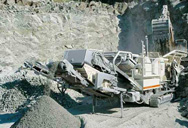
Failure rate analysis of Jaw Crusher: a case study Sādhanā
2019年1月2日 Though traditional maintenance practices exist in crushing plants, a methodical analysis of failure trend is imperative to improve operational reliability of this critical equipment. The present paper deals with failure analysis of rock crusher and its critical components using total time on test (TTT)-plot and other statistical tools.2018年3月15日 Listed below are three completely different types of crusher maintenance that must be thoroughly understood regardless of the crusher type being used. Preventive Implementing a preventive maintenance program is the best method of keeping a crusher in good operating condition for a long period.Understanding three different types of crusher maintenance2014年2月25日 A cone crusher is used in mineral processing plant as a secondary or tertiary type rock crusher. In this case study, explored the general objective of the failure modes and effects analysis (FMEA) and FTA analysis work is to evaluate the application impact of the reliability centered maintenance (RCM) methodology on a power Reliability centered maintenance of cone crusher: a case study
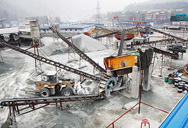
Preventive crusher and screen maintenance - Metso
Fully utilizing the latest preventive crushing and screening machine maintenance technology can help save aggregates production business owners big money annually. After all, crushers and screens are critical assets that keep their businesses running smoothly and efficiently. Lokotrack® ST3.5™ mobile screen.2023年9月2日 Crushing plant downtime can cause significant financial loss. Discuss the importance of effective planning of scheduled maintenance downtime to minimise production disruptions. Explain the benefits of a detailed maintenance schedule, coordination with suppliers and availability of necessary spare parts.Maintenance and Optimization of Crushing Plants: 2014年5月14日 The article presents a method to combine crushing plant simulation and optimisation with quality and economic considerations in order to successfully study alternative configurations of the...Field monitoring and performance evaluation of crushing plant
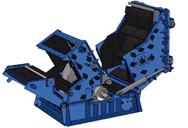
Preventive Maintenance Scheduling by Modularity Design
2020年1月1日 In effort to remedy this, this article considers relevant maintenance issues at early stages of product development and presents a novel modular methodology based on the simultaneous...2023年10月26日 The seven critical maintenance items discussed in this article, including lubrication systems, conveyor belts, crusher components, screening components, electrical systems, dust control and suppression, and emergency systems, are essential for keeping mobile crushing plants operational, efficient, and safe.Seven Critical Maintenance Items For Mobile Crushing Plants ...2018年12月26日 Information about crushing technology, construction, working and maintenance of crushers for bulk materials is given in this article. Crushing Technology. There are four basic ways to reduce size of a material: by impact, by compression, by shear or by attrition. Most crushers employ a combination of all these crushing methods.Construction, Working and Maintenance of ... - Practical
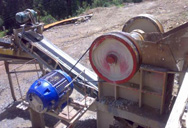
Reliability centered maintenance of cone crusher: a case
2017年8月24日 The Reliability of the crusher influences the productivity of the plant. The purpose of this paper is to focus the application of reliability centered maintenance with an aim to improve the reliability of the cone crusher. reliability tools failure modes and effects analysis and total time to test-Plot are explored in support of the study.2019年1月2日 Though traditional maintenance practices exist in crushing plants, a methodical analysis of failure trend is imperative to improve operational reliability of this critical equipment. The present paper deals with failure analysis of rock crusher and its critical components using total time on test (TTT)-plot and other statistical tools.Failure rate analysis of Jaw Crusher: a case study Sādhanā2018年3月15日 Listed below are three completely different types of crusher maintenance that must be thoroughly understood regardless of the crusher type being used. Preventive Implementing a preventive maintenance program is the best method of keeping a crusher in good operating condition for a long period.Understanding three different types of crusher maintenance
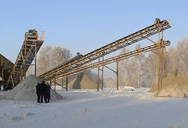
Reliability centered maintenance of cone crusher: a case study
2014年2月25日 A cone crusher is used in mineral processing plant as a secondary or tertiary type rock crusher. In this case study, explored the general objective of the failure modes and effects analysis (FMEA) and FTA analysis work is to evaluate the application impact of the reliability centered maintenance (RCM) methodology on a power Fully utilizing the latest preventive crushing and screening machine maintenance technology can help save aggregates production business owners big money annually. After all, crushers and screens are critical assets that keep their businesses running smoothly and efficiently. Lokotrack® ST3.5™ mobile screen.Preventive crusher and screen maintenance - Metso2023年9月2日 Crushing plant downtime can cause significant financial loss. Discuss the importance of effective planning of scheduled maintenance downtime to minimise production disruptions. Explain the benefits of a detailed maintenance schedule, coordination with suppliers and availability of necessary spare parts.Maintenance and Optimization of Crushing Plants:
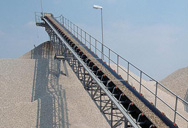
Field monitoring and performance evaluation of crushing plant
2014年5月14日 The article presents a method to combine crushing plant simulation and optimisation with quality and economic considerations in order to successfully study alternative configurations of the...2020年1月1日 In effort to remedy this, this article considers relevant maintenance issues at early stages of product development and presents a novel modular methodology based on the simultaneous...Preventive Maintenance Scheduling by Modularity Design 2023年10月26日 The seven critical maintenance items discussed in this article, including lubrication systems, conveyor belts, crusher components, screening components, electrical systems, dust control and suppression, and emergency systems, are essential for keeping mobile crushing plants operational, efficient, and safe.Seven Critical Maintenance Items For Mobile Crushing Plants ...
- كسارة الفك صغيرة لالكوارتز
- معدات المناولة الثقيلة
- iron ore extraction process 42 orecrusherplant
- قیمت سنگ منگنز در هر تن
- mobile wheel mounted iron ore crusher
- كيفية بناء كسارة الصخور الصغيرة التي تعمل بالطاقة اليدوية
- شركة منجم الذهب والصناعة
- portables fraiseuses d'or pour le sable Concasseurs du beton
- شركهالتنميه لتجهيزاتالصناعيه قسم المعدات الثقيله
- مطحنة فرس النهر للبيع في جنوب أفريقيا
- مصنع الذهب المحمول للبيع أستراليا
- سنگ شکن کارخانه سنگ زنی پودر باریت
- lump iron ore beneficiation process
- كسارات حجر الفكين
- كسارة متنقلة تستخدم أساسا لمعالجة طحن خام المنغنيز
- ناقلات السيور الناقلة
- مينجيلولا كيراغامان دالام إندستري بيرتامبانجان
- تولید کنندگان مجموعه سنگ شکن سنگی
- مطاحن قضيب لطحن البوكسيت
- الكرة مطحنة الذهب الانتعاش